Working Safely on Farm Building Roofs
Date published:
Too many falls from farm building roofs result in serious injury, disruption to farm business activity, additional indirect costs and sadly on occasions, a grieving family.
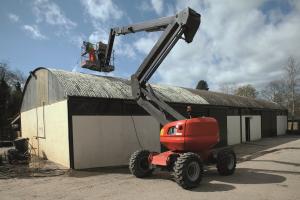
These events are avoidable if some thought and planning goes into the project before the physical work starts in the farmyard.
In fact there is a legal requirement on those persons in control of such work (duty holders) to do exactly this. The “Construction, (Design and Management) Regulations (Northern Ireland) 2016” which are more commonly referred to as the “CDM Regs”, sets out the duties of all involved. The legislation applies to all construction work – large or small, on farm or in other settings.
The farmer or farm business initiating the project (known as the “client”) must consider who will be awarded the contract to construct it. Whether it is a new building, a building repair job, a roof replacement or work that involves some dismantling or demolition, it is very important that consideration is given to the choice of contractor in terms of
- his experience and competence to carry out and manage the type of work to be done
- his ability to provide the plant and equipment required to complete the work safely
- the workforce (employees or self-employed sub-contractors) having the necessary skills and competence for the type of work
- his general attitude towards health and safety
Having discussed the job, (ideally on location) with the chosen contractor, he should be asked for an appropriate method statement, drawn up for the specific work to be done, before work starts. This should satisfy the farmer that the job will be done in compliance with good health and safety practice.
The contractor or principal contractor (if there are several contractors involved) needs to fully understand the job to be done. This means liaising with the farmer over access, understanding any limitations due to other farm work activity, agreeing on shared equipment or workforce, etc. The principal contractor is responsible for all health and safety around his construction work activity, even though others have responsibilities also. Where the farmer directly engages more than one contractor for the project, then the farmer takes on the roles of a principal contractor. The work starts with planning and then drawing up a method statement to be agreed with the client.
For working on roofs, the correct choice of plant and equipment is a key element of the planning. The “Work at Height Regulations (Northern Ireland) 2005” is very clear on the hierarchy of control measures to minimise risk from falls.
- The amount of time spent working at height should be minimised if possible
- Where it is necessary to work at height, then working from a safe platform is the preferred option. This could be properly erected fixed or mobile scaffold, or some form of mobile elevating work platform (MEWP), depending on the circumstances.
The use of farm loader buckets or pallets on the forks of a fork lift truck or non-integrated safety cages attached to a telehandler and other such “make–do” methods are not acceptable. For a variety of reasons these methods can lead to serious accidents. Some telehandlers are designed to take safety cage attachments which are integrated with the base machine i.e. controls in the safety cage are able to be connected into the telehandler hydraulics to allow control by an operative in the safety cage. These are acceptable in appropriate circumstances.
Specific formal training for operators of any form of telehandler or MEWP is essential.
- Where it isn’t possible to work from a safe platform (e.g. where the top side of a roof has to be accessed) then systems to mitigate the consequences of a fall, should be carefully considered. Close hung safety netting or airbags are methods now widely available. Where work on fragile roofs (e.g. asbestos cement or badly corroded metal sheets), work at or near roof lights or to protect from fall risk at the leading edge when sheeting a roof, etc. these types of passive system must be used. They must be installed by competent individuals.
- Fall arrest harnesses are only suitable for use in very limited circumstances and because they are personal fall protection systems (as opposed to a collective system) are low in the hierarchy of measures to be considered.
As well as considering what system will be provided to facilitate safe work at height, thought also needs to be given to how the workforce will safely access the roof work area and how any heavy items (e.g. cladding materials required) will be elevated and handled into position.
Whether the job is large or small, new work or repair work, time spent planning will help the smooth execution of the contract.
The method statement drawn up after the planning has been done will serve to inform all parties involved in the work. This does not have to be a long-winded document but rather sets out who is involved and how, what plant and equipment is required, the sequence of work and a reminder of risk control measures to be implemented.
Once the roof work begins good supervision from preparation to completion of the job should ensure everyone’s health and safety is protected.
Check out HSENI’s web site, www.hseni.gov.uk for more advice and links to other guidance which may be useful to your work planning.
October 2021