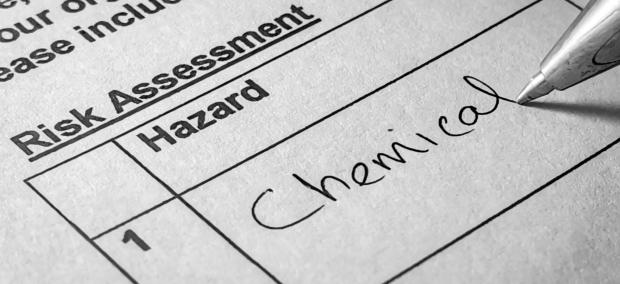
What are hazardous substances?
Many people are exposed to a variety of substances at work (for example chemicals, fumes, dusts, fibres) which can, under some circumstances, have a harmful effect on their health. These are called ‘hazardous substances’. Exposure to chemicals or other hazardous substances at work can put people’s health at risk if not properly controlled, causing diseases which include asthma, dermatitis or cancer.
Where do the Regulations apply?
COSHH covers chemicals, products containing chemicals, fumes, dusts, vapours, mists, gases, and biological agents (germs). If the packaging of a substance or chemical has any hazard symbols displayed, then it is classed as a hazardous substance, but remember that health hazards are not limited to substances labelled as 'hazardous'. Some harmful substances can be produced by the process you use, for example:
- wood dust from sanding
- silica dust from tile cutting
- fumes from welding
COSHH also covers:
- asphyxiating gases
- bacteria that cause diseases, such as Leptospirosis or Legionnaires Disease
- other bacteria used in laboratories
COSHH does not cover Lead, Asbestos or Radioactive Substances, as they have their own specific Regulations.
Substances used in the workplace can cause employees immediate harms whilst some health effects may not become apparent for many years. Effects can range from skin irritation to developing cancer depending on the type and duration of exposure. There are also many routes of admission into the body by chemicals and substances. These include inhalation, adsorption through the skin, ingestion or injection.
Depending on the substance or chemical workers are exposed to, they can lead to many different health effects. These include
- skin irritation, dermatitis or skin cancer
- burns
- asthma due to sensitisation
- lung diseases, including COPD, asthma
- death due to cancer, asphyxiation
The Control of Substances Hazardous to Health Regulations (Northern Ireland) 2003, (COSHH NI) require employers to control substances that can harm workers' health.
To prevent or reduce workers' exposure to hazardous substances employers must:
- assess the risks associated with the work process, deciding how to prevent harm to health
- identify the hazard by finding out what the health hazards associated with a chemical/substance or process are
- provide adequate control measures to reduce harm to health
- make sure control measures are used correctly
- keeping all control measures in good working order
- providing information, instruction and training for employees and others
- provide adequate supervision to ensure control measures are used correctly
- providing monitoring and health surveillance when required
- plan for emergencies
A document entitled COSHH NI: A Brief guide to the Regulations has been produced by HSENI, informing employers what they need to know about COSHH NI. This document is free to download.
Risk assessment
As an employer, you are required by law to protect your employees, and others, from harm. This can be done by completing a risk assessment.
Risk assessments must be undertaken by a competent person who has sufficient skills, knowledge and experience with the chemicals and process to be undertaken.
Details of chemical properties of substances used by your organisation are available via the Safety Data Sheets (SDS). These are important documents in the safe supply, handling and use of chemicals. They help ensure that those who use chemicals in the workplace do so safely without risk of harm to themselves, others or the environment.
The SDS contains the information necessary to allow employers to undertake a risk assessment as required by COSHH NI. The SDS itself is not an assessment of the risk.
The SDS provides important information to the user including details of health effects, exposure limits, what to do in the event of an emergency, and the PPE or RPE for safe handling and use. Employers should use the contents of the SDS to develop their COSHH risk assessment. HSE GB have developed a number of example risk assessments that organisations can use to assist in understanding what an assessment could look like:
How do I assess the risks properly?
Identify the hazards
Identify which substances are harmful by reading the product labels and safety data sheets (SDS). If in doubt, contact your supplier.
It is also important to consider harmful substances which may be produced by the processes, such as cutting or grinding, or to which workers may be otherwise exposed. Examples include:
- processes that emit dust, fume, vapour, mist or gas into the work environment
- skin contact with liquids, pastes and dusts
HSE have produced a list of substances which have workplace exposure limits (WELs) as they are hazardous to health. WELs are British occupational exposure limits and are set in order to help protect the health of workers.
Assess the risks
Decide who might be harmed and how.
Think about:
- how workers might be exposed (whether the substance can be inhaled, get onto or through the skin or ingested) and the effects of exposure by each of these routes
- how often people work with the substance and for how long
- anyone else who could be exposed - maintenance workers, contractors and other visitors or members of the public
- what measures your organisation have already put in place to control the risks
- what further action is needed to control the risks
- who needs to carry out the action
- when the action is needed by
Control the risks
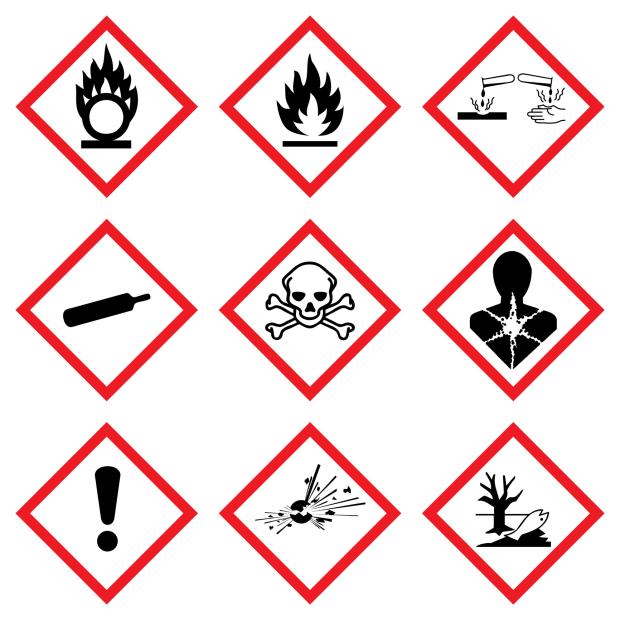
Once you have carried out a risk assessment and identified all harmful substances which are present, and how workers can be harmed, you must decide the best way to control exposure using the hierarchy of control.
There is a broad hierarchy of control options available, based on inherent reliability and likely effectiveness. COSHH NI, Regulation 7 refers to many of these options. They include:
- elimination of the hazardous substance
- modification of the substance, process and/or workplace
- applying controls to the process, such as enclosures and LEV
- ways of working which minimise exposure
- equipment or devices worn by exposed individuals
The key message is that there is a hierarchy of reliability of control options and this is often linked to their effectiveness.
Elimination
Eliminating the substance means there cannot be any exposure. Always consider elimination first.
Do you really need to use a particular substance, or is a safer alternative available?
Can you change the process to eliminate its use or avoid producing it? If this is not possible, you must put in place adequate control measures to reduce exposure.
Changing the process to reduce risks
Consider whether you can change the process you use to reduce the risk of exposure. For example, you could reduce the temperature of a process to reduce the amount of vapour getting into the air or use pellets instead of powders as they are less dusty.
Containment
Enclose the process or activity as much as possible to minimise the escape or release of the harmful substance.
Use closed transfer and handling systems and minimise handling of materials.
Use a properly designed local exhaust ventilation (LEV) system which extracts dust, fume, mist, gases or vapour through a hood or booth and reduces the exposure of the worker.
Most LEV equipment is required to be thoroughly examined and tested every 14 months by a competent person (someone who has the necessary skills, knowledge and experience to carry out the work safely), however Schedule 4 of COSHH NI outlines some exceptions to the legal, maximum intervals for thorough examination and testing (TExT) of LEV used in certain processes. Also, where wear and tear of an LEV system is liable to mean that its effectiveness will reduce between tests then TExT should be carried out more frequently.
Systems of work
Restrict access to only those who need to be involved in the work process.
Plan the storage of materials and use appropriate containers. Check that storage containers are correctly labelled and that incompatible materials, for example acids and caustics are separated.
Plan the storage and disposal of waste.
Cleaning
Exposure to hazardous substances can occur during cleaning processes, so plan and organise the workplace so that it can be easily and effectively cleaned. Smooth work surfaces will allow easy cleaning.
Have the right equipment and procedures to clear up spillages quickly and safely.
Clean regularly using a 'dust-free' method - vacuum, wet sweeping. Air lines should be avoided as they disperse potentially harmful materials over a large area, affecting others.
Personal protective equipment (PPE)
If you cannot adequately control exposure by other means, provide personal protective clothing and equipment, in combination with other control measures.
Do not automatically opt for PPE as a control measure. It is not as reliable or effective as other measures.
Information and training
Workers need to understand the outcome of your risk assessment and what this means for them. Tell them what the hazards and risks are, and any workplace exposure limits, and what they need to do to protect themselves and others.
You must make workers aware of the results of any monitoring of exposure and the collective results of health surveillance.
Train workers to use controls and PPE correctly.
Workers should know what to do if there is an accident (for example spillage) or emergency.
Contractors in your workplace also need to know what the risks are and how you are controlling them. In addition, you need to know if they are bringing hazardous substances onto your premises, and how they will prevent harm to your workers.
Record your findings
If you have five or more employees, you must record your assessment but, even if you have fewer than five, it makes sense to write down what steps you have taken to identify the risks. Make a list of the actions you have taken to control the risks to workers' health.
Review your controls
Review the risk assessment regularly to ensure it is kept up to date and accounts for any changes in your workplace.
You must review the controls you have put in place to make sure they are working.
You should also review them if they may no longer be effective or there are changes in the workplace that could lead to new risks such as changes to:
- staff
- a process
- the substances or equipment used
Also consider a review if your workers have spotted any problems or there have been any accidents or near misses.
Update your risk assessment record with any changes you make and inform your employees of these changes.
Workplace exposure limits
As an employer, you must protect workers from exposure to hazardous substances.
Where substances have been classified as carcinogens, mutagens or asthmagens, to comply with the Control of Substances Hazardous to Health (Northern Ireland) Regulations 2003 (COSHH NI), exposure must be controlled to as low as is reasonably practicable (ALARP).
Workplace exposure limits (WELs) are GB occupational exposure limits approved by HSE. They are set to help protect workers’ health. WELs are concentrations of hazardous substances in the air, averaged over a set period of time.
Find WELs in EH40
Many thousands of substances are used at work but only about 500 substances have WELs. EH40 Workplace exposure limits is a publication which contains a list of all current GB WELs. The list is legally binding under COSHH NI.
Monitor WELs
You can check that exposure to hazardous substances is below their WEL by monitoring. This means measuring the substance in the air that a worker breathes while they are undertaking a task.
You may get a consultant to monitor substances in your workplace. Exposure measurement: Air sampling G409 (PDF) tells you what to expect from a competent consultant who provides monitoring services.
Monitoring can be a useful indicator to check whether the control measures you have in place are effective. If they are, exposures are likely to be below the WEL.
Health surveillance
The purpose of health surveillance is for the employer to gather information about employees’ health which helps to protect employees from risks to health in the workplace.
Health surveillance is required when:
- There is a disease associated with the substance in use
- It is possible to detect the disease or adverse change and reduce the harm
- Workplace conditions make it likely that the disease will appear
Forms
Sometimes you will be required to submit certain information to HSENI. The current list of forms are listed below:
Resources
- EH40/2005 Workplace Exposure Limits - (hse.gov.uk)
- HSENI Leaflet - COSHH (NI) A Brief Guide to the Regulations
- L005 Control of Substances Hazardous to Health - (hse.gov.uk)
Key Legislation
- Control of Substances Hazardous to Health Regulations (Northern Ireland) 2003 - (legislation.gov.uk)
Please note that this link is to the original legislation, visitors should verify for themselves whether legislation is in force or whether it has been amended or repealed by subsequent legislation.
Useful links
- Appointed doctors
- Asthma
- Candles and CLP
- Chemicals
- Flour Dust
- Isocyanates
- Labelling for chemical products - information for duty holders
- LEV (local exhaust ventilation)
- Metalworking fluids
- Nanomaterials
- Skin
- Welding Fume
- Welding Fume - Common Questions and Answers
- Respiratory Protective Equipment (RPE)
- Guidance on the compilation of safety data sheets